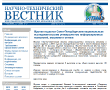
IDENTIFICATION OF PIEZOACTUATOR PARAMETERS
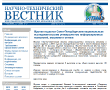
Annotation
The paper presents a version of technical implementation of automated installation and its performance algorithms for determining the piezoactuator parameters. The evaluation was carried out by a linear regression form of transfer function. The first approximations were used as the derivatives. The known parameters of the piezoactuator were used to analyze identification procedure results and determine the object parameters. A stepwise action was applied to the input in the first method. In this case, it is necessary to perform measurements with a frequency more than 200 kHz to ensure an error less than 1%. The paper deals with the problems related to making measurements in real time mode and to processing large amounts of data. The feature of the piezoactuator operation was used to improve the quality of the procedure – its ability to direct acceleration measurement. Also, a pulse width modulated signal with a variable duty cycle was formed to obtain a more informative output signal. The conclusion was drawn that the application of the least-squares method in conjunction with the pulse-width input action and the usage of the accelerometer makes it possible to obtain results with a small error in the estimation even when operating at sampling frequencies near 20 kHz. The embedded System Identification Toolbox enables accurate determination of a model on 20 kHz frequency, technically realizable in real time mode. As a result, the variant of technical implementation of automated installation and performance algorithms were proposed. The parameters convergence was provided with an accuracy of 0.5% at measurement frequency of 20 kHz that allows for real-time operation in MATLAB Simulink Desktop Real-Time software.
Keywords
Постоянный URL
Articles in current issue
- ON MODERN APPROACH TO AIRPLANE-TYPE UNMANNED AERIAL VEHICLES DESIGN WITH SHORT TAKEOFF AND LANDING
- SEARCH AUTOMATION OF BINARIZATION OPTIMUM LEVEL FOR SYNTHESIZED HOLOGRAMS
- INSCRIPTION PROCESS RESEARCH AND OPTIMIZATION FOR SUPERIMPOSED FIBER BRAGG GRATINGS
- SPATIALLY SELECTED SPECKLE-CORRELOMETRY OF TEMPERATURE DEPENDENT GELATION KINETICS
- CONVERGENCE SPEED INCREASE OF A FINITE-TIME STABLE CONTROL SYSTEM
- ROBUST PROPERTIES OF SYSTEMS WITH NEGATIVE DEGREE OF HOMOGENEITY WITH RESPECT TO DELAY
- COMPUTER SIMULATION OF INTERACTION OF LYSINE DENDRIMERS WITH STACK OF AMYLOID PEPTIDES
- INVESTIGATION ON CORRECTING PROCESS OF SPHERICAL ROTOR IMBALANCE AT THIN FILM DEPOSITION STAGE
- ALGEBRAIC MANIPULATION DETECTION CODES WITH PERFECT NONLINEAR FUNCTIONS UNDER NON-UNIFORM DISTRIBUTION
- DISTRIBUTION OF RESOURCES BASED ON HYBRID MODELS OF SWARM INTELLIGENCE
- SHAPE RESTORATION OF THREE-DIMENSIONAL OBJECT FROM TWO-DIMENSIONAL IMAGES
- AUTOMATED SIMULATION TECHNOLOGY OF MULTI-HOP WIRELESS NETWORKS IN HETEROGENEOUS MODELING ENVIRONMENT
- VARIANT OF ODOR SYSTEM FOR THREATS RECOGNITION
- ADAPTIVE SELECTION OF ARTIFICIAL IMMUNE SYSTEMS AND LOCAL SEARCH MUTATION OPERATORS
- NONLINEAR DYNAMICS AND STABILITY OF MICROSYSTEMS ENGINEER-ING ELEMENTS
- SPECIAL DESIGN ASPECTS OF GRIPPING DEVICES FOR INCREASING THE FLEXIBILITY OF AUTOMATED AND ROBOTIC MANUFACTURING LINES AT INSTRUMENT MANUFACTURING FACILITIES
- AN APPROACH TO RELIABILITY INCREASE OF TURBINE SAFETY SYSTEM BASED ON HIDDEN RESERVES
- OPERATIONAL CONTROL METHOD FOR TRAIN INTEGRITY MONITORING BASED ON OPTICAL COHERENT REFLECTOMETRY DATA
- LOWER LIMB EXOSKELETONS: BRIEF REVIEW
- MODELING OF LOCOMOTOR SYSTEM DYNAMICS
- EXPERIMENTAL INVESTIGATION OF WINDING DIAMETER EFFECT ON OPTICAL PROPERTIES OF HI-BI FIBER WITH TIN COATING
- DIGITALIZATION OF PROJECT AND PRODUCTION PROCEDURES AS A TOOL FOR INSTRUMENTATION DESIGN AUTOMATION IN INDUSTRY 4.0