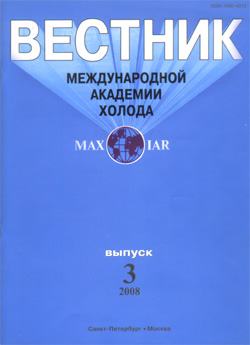
Swirling vapour flow in short linear heat pipes. Part I
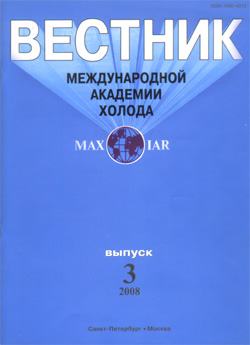
Annotation
The article presents the results of the experimental studies of heat transfer coefficients KHP for short linear heat pipes (HP’s) with a Laval nozzle-liked vapour channel and with a partially swirled vapour flow inside the channel. A partial azimuthal swirling of the jet vapour stream is created using inclined injection channels of 1 mm diameter in a flat multilayer mech evaporator, with an inclination angle φ relative to the longitudinal axis in the azimuthal direction in the range of 0° < φ < 60°. An analysis of the recommended vapour channel shape, carried out by the estimating of the Richardson number Ri of the vapour flow jets above the evaporator, allowed us to estimate the value of the dimensionless longitudinal radius of curvature δ/Rconf for the confuser part of the vapour channel, which is determined from the condition of minimal friction losses during the flow of moist vapour in the boundary layer δ along the concave wall of the confuser part in the vapour channel with a longitudinal radius of curvature Rconf. The concave diffuser part shape of the vapour channel is determined by the condition that the moving vapour jets’ velocity vectors must be parallel to the longitudinal axis of the diffuser part of the HP’s vapour channel.The results of the numerical simulation for the hydraulic resistance coefficients ξvp of the HP’s vapour channel closed with flat lids at partially swirling jet vapour flow, obtained by using the ANSYS FLUENT software, show a decrease in ξvp coefficients at high values of the evaporator temperature load, in the range of vapour flow velocities of 1 m/s < uz ≤ 100 m /s, and in the range of swirling angles of 0°<φ<30°. With the increasing the swirling angles φ>30°, a sharp increase in the hydraulic resistance coefficient ξvp occurs. The heat transfer coefficients KHP for a set of the identical HP’s with a different inclination angles φ of the injection channels in the evaporators, with the same working fluid mass filling (δm/m ≤ 0.1%), represent an extreme convex function depending on the magnitude of inclination angle φ in the injection channels, with a maximum at the swirled angle of the vapour flow φ = 26°±2°. The magnitude of the excess of the KHP with a swirling vapour flow over the identical HP’s with a direct vapour flow reaches 10%.
Keywords
Постоянный URL
Articles in current issue
- Refrigeration supply systems based on lithium bromide absorption refrigerating machines
- Heat transfer intensity of heat exchangers with plate fins
- The efficiency of the methods for regulating the capacity of scroll compressor as a part of the refrigeration system
- The scheme of liquefied carbon dioxide production by membrane separation with recirculation system
- Energy modeling and experimental validation of heat pump operating modes in exhaust air heat recovery. Part 2. Energy, economic and environmental indicators
- The process of fat extraction from fish processing waste as a raw material for biotechnological synthesis of polyhydroxyalkanoates
- Quick-freezing of raw-materials of animal origin using cryogenic technologies
- Influence of ultrasound on freezing and the quality of frozen fruits and vegetables
- Enzymatic hydrolysis of integumentary tissues of pike perch
- Fundamental equation of state for propylcyclohexane